Аннотация: превосходная высокая надежность керамической подложки, покрытой медью из нитрида кремния, делает ее одним из наиболее перспективных материалов для силовых модулей высокоскоростного железнодорожного транспорта, электромобилей и других областей. В настоящее время только японские производители имеют массовые производственные мощности, а импорт на внутреннем рынке затруднен, что препятствует развитию смежных отраслей. Высокоэффективная керамическая подложка из нитрида кремния была получена путем спекания под давлением воздуха, а керамическая подложка из нитрида кремния, покрытая медью, была получена путем активной пайки металлов. Прочность на изгиб керамики из нитрида кремния составляет 800 МПа, а трещиностойкость составляет 80 МПа · м ½,Теплопроводность 90 Вт/ (м · К), прочность на разрыв переменного тока 40 кВ/мм и объемное удельное сопротивление 3 семь × 1014 Ом · см; Прочность на отрыв керамической подложки из нитрида кремния, покрытой медью, достигает 130 н/см. При циклическом воздействии высоких и низких температур -45 ~ 150 ℃ время удара керамической подложки, покрытой медью из нитрида кремния, в 10 и 100 раз превышает время удара нитрида алюминия и подложки, покрытой глиноземом, соответственно; при толщине меди 0 32 мм/0. Время удара 25 мм до 5000 раз и толщине меди 0,5 мм 5 мм/0. Когда время удара 5 мм достигает 1000 раз, образцы остаются неповрежденными; в меди толщиной 0 8 мм/0. Когда время удара 8 мм достигло 500 раз, на образце все еще не было микротрещин и других дефектов, которые отличались от толщины меди 0,5 мм 32 мм/0. Время цикла подложки, покрытой медью из нитрида алюминия, то же самое и составляет 25 мм; надежность керамической подложки из нитрида кремния, покрытой медью, очевидно, выше, чем у существующих изделий. Ключевые слова: керамика из нитрида кремния; медная подложка; активная пайка металлов; надежность; силовое устройство 0 Введение Для решения все более серьезных экологических проблем электроэнергетика как экологически чистая энергия стала центром внимания во всем мире, а электрификация использования энергии стала направлением развития. При применении электроэнергии мощные электронные устройства (такие как биполярный транзистор с изолированным затвором IGBT) являются основой для управления и преобразования энергии. Они широко используются в области высокоскоростных железных дорог, интеллектуальных сетей, электромобилей и нового энергетического оборудования
[1-2]. С увеличением плотности энергии силовые устройства предъявляют все более высокие требования к теплоотдаче и надежности керамической подложки, покрытой медью. В настоящее время материалы керамических медных подложек для силовых устройств в основном включают оксид алюминия (Al2O3), нитрид алюминия (AlN) и нитрид кремния (Si3N4) [3-4]. Подложка, покрытая медью Al2O3, в основном изготавливается из меди с прямыми связями (DBC) [5-6]. Он имеет низкую теплопроводность и ограниченную способность рассеивать тепло. В основном он используется в областях с низкой удельной мощностью и без строгих требований к надежности. Подложка, покрытая медью AlN, в основном использует процесс пайки активными металлами (AMB) с более высокой надежностью. Благодаря высокой теплоотводящей способности подложки, покрытой медью из нитрида алюминия AMB (AlN AMB Cu), она подходит для некоторых рабочих сред с высокой мощностью и высоким током. Однако из-за относительно низкой механической прочности срок службы AlN AMB Cu при циклическом воздействии при высоких и низких температурах ограничен, область его применения ограничена. С другой стороны, по мере развития технологии подготовки силовых микросхем третьего поколения (таких как SiC и GaN) [7-8] более высокая удельная мощность и более высокая рабочая температура окружающей среды приводят к быстрому сокращению времени воздействия высокотемпературных и низкотемпературных циклов и надежности подложек, покрытых медью Al2O3 и AlN, что не может соответствовать требованиям использования. Подложка, покрытая медью из нитрида кремния AMB (Si3N4 - AMB Cu), стала одним из наиболее перспективных материалов-кандидатов благодаря своим превосходным комплексным термодинамическим свойствам, таким как высокая прочность, высокая вязкость, устойчивость к высоким температурам и высокая надежность [9-12]. Si3N4 — AMB Cu не только обладает такой же теплоотдающей способностью, что и AlN, но и срок его службы может быть увеличен более чем на порядок. Miyazakia et al. [13] исследовали циклические ударные свойства Si3N4 AMB Cu при -40 ~ 250 ℃: после 100 циклов толщина меди составила 0,5 мм В керамике возникли микротрещины в образце толщиной 3 мм, а толщина меди составляла 0,5 мм. Образец 15 мм не дал микротрещин после 1000 циклов. Фактически, Si3N4 AMB Cu использовался в некоторых моделях Toyota и Tesla. Однако в настоящее время технология приготовления высокоэффективной керамической подложки Si3N4 в основном находится в руках японских компаний, а в Китае нет мощностей по массовому производству. Поэтому сообщений об исследовании Si3N4 AMB Cu мало. Основываясь на разработке высокопроизводительной керамической подложки Si3N4, в данной статье проводится исследование по оценке надежности Si3N4 AMB Cu с целью накопления основных экспериментальных данных для широкого применения соответствующих силовых устройств в высокоскоростных железных дорогах, интеллектуальных сетях, электромобилях и других областях Китая. эксперимент 1.1 экспериментальное сырье и инструменты Сырье: керамическая подложка Si3N4, бескислородная медь, активный металлический припой. Приборы и оборудование: трафаретный принтер km-sy4060a, вакуумная паяльная печь ylm11-3020w. 1.2 Экспериментальный процесс 1. 2. 1 Получение Si3N4 — AMB Cu методом AMB Поместите керамическую подложку Si3N4 в дистиллированную воду с температурой 70 ℃, проведите ультразвуковую очистку в течение 1 минуты, смойте поверхностные загрязнения и высушите. Обе стороны подложки наносят трафаретную печать активным металлическим припоем (основным компонентом является 72ag28cu, и небольшое количество активного металла вводится в виде пасты), который сушат в духовке при 80 ℃. Покройте обе стороны подложки, напечатанной припоем с медью, поместите ее в печь для вакуумной пайки и получите образец через 800 ℃ /10-3 Па/10 мин. На рис. 1 представлена структурная схема.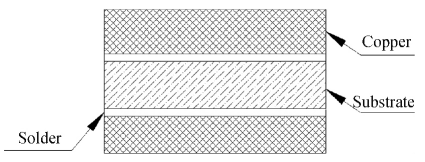