陶瓷注射成型(CIM)是通过将聚合物注射成型方法与陶瓷制备工艺相结合而开发的一种制备陶瓷零件的新工艺。与20世纪70年代开发的金属注射成型(MIM)技术类似,它们是粉末注射成型(PIM)技术的主要分支,是在相对成熟的聚合物注射成型技术的基础上开发的。对于尺寸精度高、形状复杂的陶瓷产品的批量生产,使用陶瓷粉末成型是最有利的。
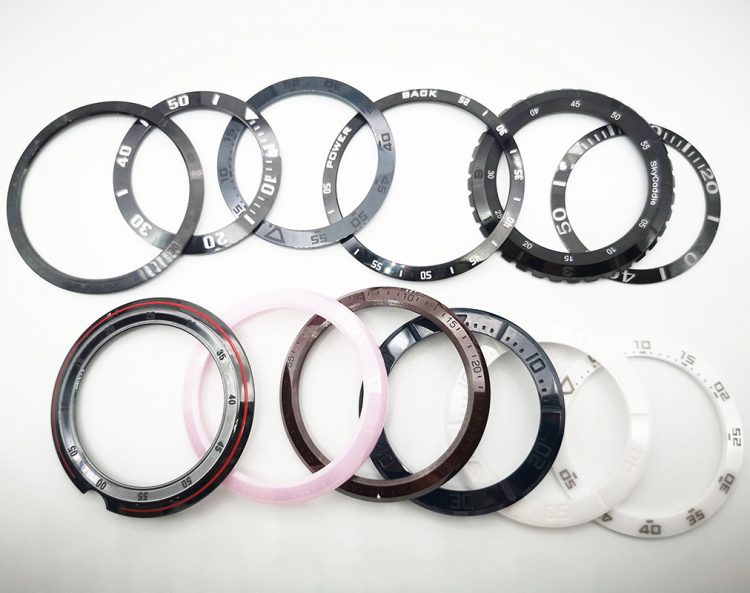
1。CIM 陶瓷注射成型技术的特点
优势: ① 成型过程具有机械化程度高、自动化程度高、生产效率高、成型周期短、毛坯强度高的特点,其过程可精确控制(程序控制),易于实现规模化、规模化生产; ② 它几乎可以对具有复杂几何形状和特殊要求的各种小型陶瓷零件进行净成型,从而使烧结的陶瓷产品无需机械加工或少加工,从而降低昂贵的陶瓷加工成本; ③ 成型的陶瓷产品具有极高的尺寸精度和表面光洁度。 缺点: 一次性设备投资和加工成本高,只适合批量生产。2。陶瓷注射成型的 CIM 工艺流程
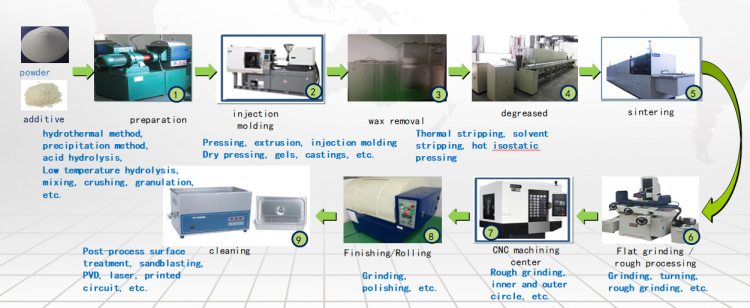
陶瓷精密注射成型的制造过程如图所示,主要包括以下四个环节:
① 喂养准备: 饲料是粉末和粘合剂的混合物。注射过程要求注射饲料具有良好的流动性,这需要选择符合要求的粉末和适当的粘合剂系统,并在一定温度下具有一定的负荷比。注射成型饲料,从而确保后续工艺的顺利进行,其产品可以从实验室走向高科技市场。因此,饲料准备在整个过程中非常关键。 ② 注塑成型和模具设计: 对注塑成型过程的控制不当会导致产品中形成许多缺陷,例如裂缝、气孔、焊缝、分层、粉末和粘合剂分离等,这些缺陷要等到脱胶和烧结后才能被检测出来。CIM 通常使用多腔模具。每个型腔的尺寸都不同,使用中型腔的磨损将导致零件尺寸的不同。此外,注射回流材料的使用会影响粘度和流变性。因此,控制和优化注塑温度、模具温度、注射压力和保压时间等成型参数对于减少绿色体重的波动、防止注塑材料中成分的分离和分离以及提高产品产量和材料利用率至关重要。 CIM技术的模具设计主要考虑注塑成型过程中模腔内进料的流量控制。由于CIM产品大多是形状复杂且精度要求高的小型零件,因此需要精心设计和布置进料口的位置、流道的长度以及排气孔的位置。当然,模具设计需要清楚地了解进料流变特性、型腔温度和残余应力分布。此外,计算机仿真技术将在粉末注射成型模具设计中发挥重要作用。 ③ 脱脂工艺: 脱脂是指从成型体中去除有机物并通过加热和其他物理方法产生少量烧结的过程。与陶瓷零件的批处理、成型、烧结和后处理相比,脱脂是注塑成型中最困难和最重要的因素。不正确的脱脂工艺方法和参数会导致产品收缩率不一致,从而导致变形、开裂、应力和夹杂物。脱脂对于后续烧结也很重要,烧结无法补偿脱胶过程中发生的裂纹和变形。粘合剂和脱脂剂结合在一起以确定脱脂方式。除了传统的热脱脂和溶剂脱脂外,当前的脱脂工艺还包括近年来开发的催化脱脂和水基提取脱脂。 ④ 烧结: 脱脂陶瓷绿色主体经过致密化并在高温下烧结,以获得具有所需外观、形状、尺寸精度和微观结构的致密陶瓷部件。由于陶瓷注射成型毛坯含有脱脂留下的孔隙,因此烧结过程中产品的收缩率相对较大,通常达到 13%-15%。可以看出,CIM技术的研究重点是烧结尺寸精度控制。此外,烧结设备也是烧结技术的关键。3。CIM 陶瓷注射成型的应用示例
目前,注射成型技术已应用于各种高性能陶瓷产品的制备。 鼎鼎致力于陶瓷粉末注射成型和制造工艺的设计、开发和生产,主要用于民用产品、移动通信、智能穿戴、手机外壳、电子烟、壳环、结构陶瓷零件等。 鼎鼎陶瓷注射成型公司产品介绍: [caption id="attachment_2861" align="alignnone" width="750"]
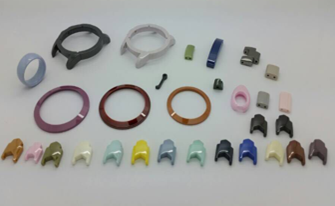
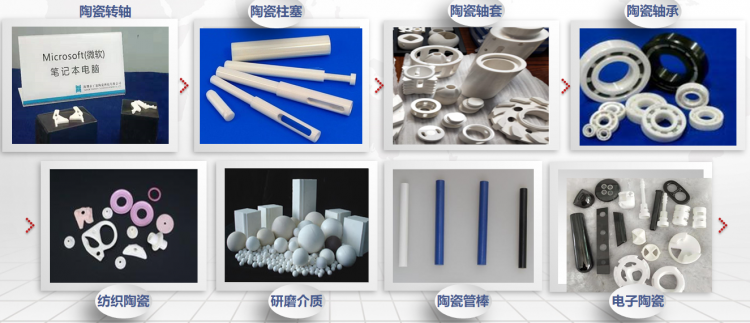