Le moulage par injection de céramique (CIM) est un nouveau procédé de préparation de pièces en céramique développé en combinant la méthode de moulage par injection de polymères avec le processus de préparation de la céramique. Tout comme la technologie de moulage par injection de métaux (MIM) développée dans les années 1970, ce sont les principales branches de la technologie de moulage par injection de poudre (PIM) et sont développées sur la base d'une technologie de moulage par injection de polymères relativement avancée. Pour la production en série de produits céramiques présentant une grande précision dimensionnelle et des formes complexes, l'utilisation du moulage en poudre céramique est la solution la plus avantageuse.
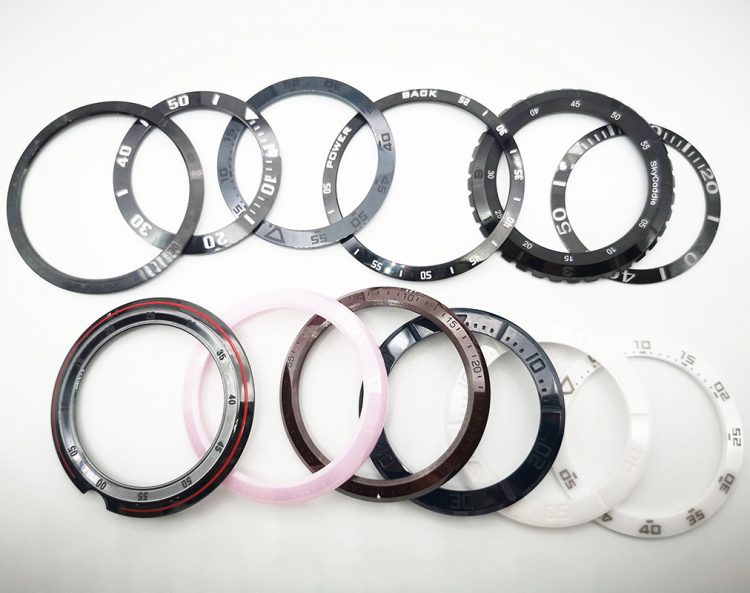
1. Caractéristiques de la technologie de moulage par injection de céramique CIM
Avantage : ① Le processus de moulage présente les caractéristiques suivantes : haut degré de mécanisation et d'automatisation, efficacité de production élevée, cycle de moulage court, résistance élevée de l'ébauche, et son processus peut être contrôlé avec précision (contrôle par programme), ce qui permet de réaliser facilement une production à grande et grande échelle ; ② Il peut presque façonner net diverses petites pièces en céramique présentant des formes géométriques complexes et des exigences particulières, de sorte que les produits en céramique frittée n'aient pas besoin d'être usinés ou moins traités, réduisant ainsi les coûts de traitement de la céramique ; ③ Les produits céramiques formés ont une précision dimensionnelle et une finition de surface extrêmement élevées. Inconvénients : Les investissements ponctuels dans l'équipement et les coûts de traitement sont élevés, et ce produit ne convient qu'à la production de masse.2. Flux de procédé CIM pour le moulage par injection de céramique
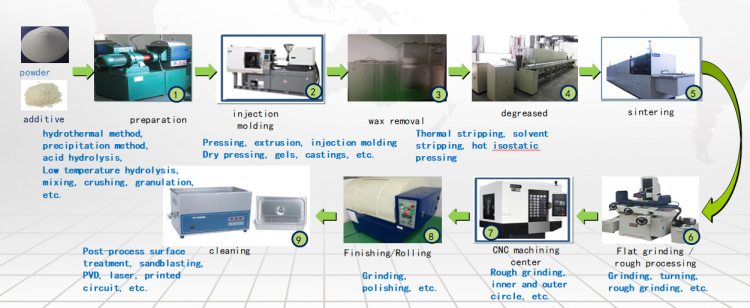
Le processus de fabrication du moulage par injection de précision en céramique est illustré sur la figure, qui inclut principalement les quatre liens suivants :
① Préparation de l'alimentation : L'alimentation est un mélange de poudre et de liant. Le processus d'injection nécessite une bonne fluidité de l'alimentation, ce qui nécessite la sélection de poudres répondant aux exigences, un système de liant approprié et un certain taux de charge à une certaine température. Les aliments pour le moulage par injection, afin de garantir le bon déroulement du processus suivant, et ses produits peuvent passer du laboratoire au marché de la haute technologie. La préparation des aliments est donc très importante dans l'ensemble du processus. ② Moulage par injection et conception de moules : Un mauvais contrôle du processus de moulage par injection peut entraîner la formation de nombreux défauts dans le produit, tels que des fissures, des pores, des soudures, un délaminage, une séparation de la poudre et du liant, etc., et ces défauts ne peuvent être détectés qu'après le déliantage et le frittage. Le CIM utilise souvent des moules à cavités multiples. Les dimensions de chaque cavité sont différentes, et l'usure de la cavité en cours d'utilisation entraînera des pièces de différentes tailles. De plus, l'utilisation d'un matériau de retour d'injection peut affecter la viscosité et la rhéologie. Par conséquent, il est crucial de contrôler et d'optimiser les paramètres de moulage tels que la température d'injection, la température du moule, la pression d'injection et le temps de maintien de la pression pour réduire les fluctuations du poids à vide, empêcher la séparation et la ségrégation des composants dans le matériau d'injection et améliorer le rendement du produit et l'utilisation des matériaux. La conception du moule grâce à la technologie CIM prend principalement en compte le contrôle du flux de matière d'alimentation dans la cavité du moule pendant le moulage par injection. La plupart des produits CIM étant des pièces de petite taille aux formes complexes et répondant à des exigences de haute précision, il est nécessaire de concevoir et d'organiser avec soin la position de l'orifice d'alimentation, la longueur de la glissière et la position du trou d'échappement. Bien entendu, la conception des moules nécessite une bonne compréhension des propriétés rhéologiques de l'alimentation, de la température de la cavité et de la distribution des contraintes résiduelles. En outre, la technologie de simulation informatique jouera un rôle important dans la conception des moules de moulage par injection de poudre. ③ Processus de dégraissage : Le dégraissage consiste à éliminer les matières organiques du corps de moulage et à produire une petite quantité de frittage par chauffage et par d'autres méthodes physiques. Comparé au dosage, au moulage, au frittage et au post-traitement des pièces en céramique, le déliantage est le facteur le plus difficile et le plus important du moulage par injection. Des méthodes de traitement et des paramètres incorrects du processus de déliantage entraînent un rétrécissement irrégulier du produit, ce qui entraîne des déformations, des fissures, des contraintes et des inclusions. Le déliantage est également important pour le frittage ultérieur, et les fissures et les déformations qui se produisent pendant le déliantage ne peuvent pas être compensées par le frittage. Le liant et le dégraissant sont liés pour déterminer le mode de dégraissage. Outre le dégraissage thermique et le dégraissage au solvant traditionnels, le procédé de dégraissage actuel inclut également le dégraissage catalytique et le dégraissage par extraction à base d'eau développés ces dernières années. ④ Frittage : Le corps vert dégraissant en céramique est densifié et fritté à haute température pour obtenir des pièces en céramique dense ayant l'apparence, la forme, la précision dimensionnelle et la microstructure souhaitées. Comme l'ébauche moulée par injection en céramique contient des pores laissés par le dégraissage, le taux de rétrécissement du produit est relativement important pendant le frittage, atteignant généralement 13 % à 15 %. On voit que l'objectif de recherche de la technologie CIM est le contrôle de la précision dimensionnelle du frittage. En outre, l'équipement de frittage est également la clé de la technologie de frittage.3. Exemple d'application du moulage par injection de céramique CIM
À l'heure actuelle, la technologie de moulage par injection est appliquée à la préparation de divers produits céramiques à haute performance. DingDing s'engage dans la conception, le développement et la production de procédés de moulage par injection de poudre céramique, principalement pour les produits civils, les communications mobiles, les vêtements intelligents, les coques de téléphones portables, les cigarettes électroniques, les bagues de boîtier, les pièces structurelles en céramique, etc. Présentation des produits de la société de moulage par injection de céramique Dingding : [caption id="attachment_2861" align="alignnone" width="750"]
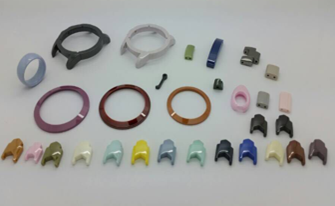
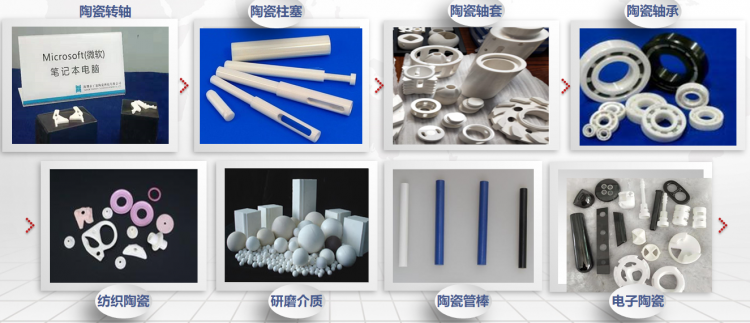